Black Silicon Carbide |
|
Black Silicon Carbide is produced in an electric resistance furnace from quartz sand and petroleum coke or anthracite at high temperature. The hardness and sharp particle shape of this material make it suitable for manufacturing of grinding wheels, coated products, wire saws, superior refractory materials and deoxideiser as well as for lapping, polishing and blasting. |
|
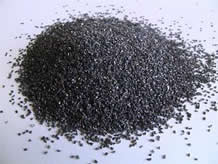 |
|
|
Chemical & Physical Properties |
Crystal Form |
Alpha SiC hexagonal system |
Chemical nature |
Slight acid |
Reaction with acids |
Very slight surface action with hydrofluoric acid |
Reaction with Alkalies |
Attcked at high temperature by alkalles and iron xide |
Oxidation-reduction effects |
Starts to oxide slowly at 800oC. No reduction |
True Density (g/cm3) |
3.20 |
Hardness |
Knoop (kg/cm2) |
2200-2500 |
Moh's |
9.5 |
Color |
Black |
Color after firing |
Black |
Decomposition point |
2200oC |
Max Usable temperature |
1540oC in air |
Specific heat (cal/g.oC) |
0oC |
500oC |
1000oC |
0.14 |
0.28 |
0.13 |
Coefficient of thermal conductivity ( cal/cm2.sec.oC) |
600oC |
800oC |
1000oC |
0.080 |
0.061 |
0.0510 |
Electrical resistivity (Wcm) |
25oC |
100oC |
400oC |
800oC |
1400oC |
50 |
46.4 |
26.6 |
7.8 |
0.65 |
Coefficient of liner expansion (x10-6) |
25oC-500oC |
25oC-1000oC |
25oC-1500oC |
25oC-2000oC |
25oC-2500oC |
4.63 |
5.12 |
5.48 |
5.77 |
5.94 |
|
|
Chemical Composition (by % weight) |
Grit |
10# - 90# |
100# -180# |
220# - 220# |
230# - 400 # |
500#-1200# |
SiC |
98.5 min |
98.0 min |
97.0 min |
96.0 min |
93.0 min |
F.C |
0.2 max |
0.3 max |
0.3 max |
0.4 max |
0.4 max |
Fe2O3 |
0.6 max |
0.8 max |
1.2 max |
1.5 max |
1.7 max |
|
|
Available grain sizes |
Grit No. |
Micron |
Grit No. |
Micron |
Grit No. |
Micron |
10 |
2360 ~ 2000 |
30 |
710 ~ 600 |
80 |
212 ~ 180 |
12 |
2000 ~ 1700 |
36 |
600 ~ 500 |
90 |
180 ~ 150 |
14 |
1700 ~ 1400 |
40 |
500 ~ 425 |
100 |
150 ~ 125 |
16 |
1400 ~ 1180 |
46 |
425 ~ 355 |
120 |
125 ~ 106 |
20 |
1180 ~ 1000 |
54 |
355 ~ 300 |
150 |
106 ~ 75 |
22 |
1000 ~ 850 |
60 |
300 ~ 250 |
180 |
90 ~ 63 |
24 |
850 ~ 710 |
70 |
250 ~ 212 |
220 |
75 ~ 53 |
|
|
Available mircron powder sizes |
|
|
|
|
|
|
|
|
|
|
|
|
|
Standard werte der Mikro-F-Reihe
|
|
|
|
|
|
|
|
|
|
|
|
|
|
|
|
|
|
|
|
|
|
|
|
|
|
|
|
|
|
|
|
|
|
|
|
|
|
|
|
|
|
|
|
|
|
|
|
|
|
|
|
|
|
|
|
|
|
|
|
|
|
|
|
|
|
|
|
|
|
|
|
|
|
|
|
|
|
|
|
|
|
|
|
|
|
|
|
|
|
|
|
|
|
|
|
|
|
|
|
|
|
|
|
|
|
|
|
|
|
|
|
|
|
|
|
|
|
|
|
|
|
|
|
|
|
|
|
|
|
|
|
|
|
|
|
|
|
|
|
|
|
|
|
|
|
|
|
|
|
|
|
Non-abrasive SiC (TN) (% by weight) |
|
Chemical Composition |
Type |
SiC min |
F.C max |
Fe2O3 max |
Size mm |
TN98 |
98.0 |
1.0 |
0.5 |
50-0
13-0
10-0
5-0
0.5-0 100#-0
220#-0 |
TN97 |
97.0 |
1.5 |
0.8 |
TN95 |
95.0 |
2.5 |
1.0 |
TN90 |
90.0 |
3.0 |
2.5 |
TN88 |
88.0 |
3.5 |
3.0 |
TN85 |
85.0 |
5.0 |
3.5 |
TN60 |
60.0 |
12.0 |
3.5 |
TN50 |
50.0 |
15.0 |
3.5 |
|
|
Applications |
Vitrified tools |
Lapping |
Resinoid tools |
Blasting |
Polishing |
Investment casting |
Tumbling |
Wear resistance |
Self-tumbling |
Refractory |
Lapping compound |
Wire saw |
Electrical |
Ceramic |
Electronic |
Nuclear |
|
 |
Tel/Fax: + 86 755 83660116, info@kaiteindustry.cn, szkaite@hotmail.com
Copyright Kaitexin All rights reserved. |
 |
|